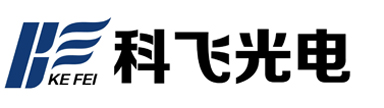
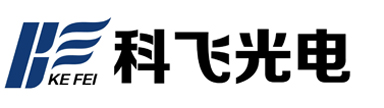
The characteristics of CNC machining technology and the steps of CNC machining parts
Edit:2025-01-22 15:52:16
The CNC machining process also follows the cutting rules of mechanical processing, which is generally the same as the machining process of ordinary machine tools. Due to its application of computer control technology in automated machining, it has the characteristics of high machining efficiency and high precision. The machining process has its advantages, with complex procedures and detailed and meticulous step arrangements.
The CNC machining process includes the selection of cutting tools, determination of cutting parameters, and design of cutting process routes. The CNC machining process is the foundation and core of CNC programming. Only with a reasonable process can high-quality and efficient CNC programs be developed. The standard for measuring the quality of a CNC program is: * less processing time, * less tool wear, and producing * best * workpieces.
The CNC machining process is a part of the overall machining process of the workpiece, or even a single process. It needs to coordinate with other preceding and succeeding processes to ultimately meet the assembly requirements of the overall machine or mold, so as to produce qualified parts.
The CNC machining process is generally divided into rough machining, medium rough corner cleaning machining, semi precision machining, and precision machining steps.
Numerical Control Programming for CNC
Numerical control programming is the entire process from part drawings to obtaining numerical control machining programs. Its main task is to calculate the cutter location point (CL point) in the machining process. The tool position is generally taken as the intersection point between the tool axis and the tool surface, and in multi axis machining, the tool axis vector is also given.
Numerical control machine tools are programmed in the form of specified numerical control codes based on the requirements of workpiece drawings and machining processes, including the movement, speed, and sequence of actions of the tools and components used, spindle speed, spindle rotation direction, tool clamping, tool loosening, and cooling operations, and input into a dedicated computer for the machine tool. Then, the CNC system compiles, calculates, and processes the input instructions, outputs various signals and instructions, and controls each part to process workpieces of different shapes according to specified displacements and sequential actions. Therefore, the programming has a great impact on the efficiency of CNC machine tools.
Numerical control machine tools must input instruction codes representing various different functions into the numerical control device in the form of programs, which are processed by the numerical control device and then emit pulse signals to control the operation of various moving parts of the numerical control machine tool, thereby completing the cutting of parts.
At present, there are two standards for CNC programs: ISO from the International Organization for Standardization and EIA from the American Electronics Industry Association. Our country adopts ISO codes.
With the advancement of technology, 3D numerical control programming generally rarely uses manual programming and instead relies on commercial CAD/CAM software.
CAD/CAM is the core of computer-aided programming systems, with main functions including data input/output, calculation and editing of machining trajectories, setting of process parameters, machining simulation, post-processing of CNC programs, and data management.
At present, Mastercam, UG, Cimatron, PowerMILL, CAXA and other powerful CNC programming software that are highly favored by users in China. The principles, graphic processing methods, and machining methods of numerical control programming are similar in various software, but each has its own characteristics.
The steps of CNC machining parts
1. Analyze the part drawing to understand the general condition of the workpiece (geometric shape, workpiece material, process requirements, etc.)
2. Determine the CNC machining process for the parts (machining content, machining route)
3. Perform necessary numerical calculations (coordinate calculation of base points and nodes)
4. Write a program sheet (different machine tools may vary, follow the user manual)
5. Program verification (inputting the program into the machine tool and performing graphic simulation to verify the correctness of the programming)
6. Processing workpieces (good process control can save time and improve processing quality)
7. Workpiece acceptance and quality error analysis (inspect the workpiece, pass it to the next process. If it is not qualified, identify the cause of the error and correct it through quality analysis).
a. Adaptive control technology for processing;
b. Intelligent optimization and selection of processing parameters;
c. Intelligent fault self diagnosis and self repair technology;
d. Intelligent fault replay and fault simulation technology;
e. Intelligent communication servo drive device;
f. Intelligent 4M CNC system: Integrating measurement, modeling, machining, and machine operation (i.e. 4M) into one system during the manufacturing process.
Phone: 19975811078
Address: 340 Jingyue Street, Economic Development Zone, Changchun City
Record number: Ji ICP No. 2023001013
Phone: 19975811078 Address: No. 340 Jingyue Street, Economic Development Zone, Changchun City Record number: Ji ICP No. 2023001013